Première partie - La Nature N° 3064 - 15 décembre 1940
Il n’est pas douteux que le bois fut le premier combustible connu de l’homme, mais très vite celui-ci a-t-il dû comprendre que la braise rouge couverte de cendres permettait de conserver du feu assez longtemps et que, si elle s’éteignait et noircissait, il était facile de réallumer celle matière noire ; c’est bien ainsi que procède certaine peuplade dans la préhistoire romancée de J.-H. Rosny, « La Guerre du feu ». Mais combien de siècles a-t-il fallu pour arriver à la meule charbonnière encore utilisée actuellement !
Quoi qu’il en soit, si nous nous en rapportons à l’Histoire naturelle de Pline, les Égyptiens étaient versés dans l’art de carboniser le bois en meules et savaient recueillir une « poix liquide » qui, en Syrie, était appelée « huile de cèdre » : les Égyptiens se servaient de cette huile pour embaumer les corps des défunts. La construction de la meule, décrite par Pline, diffère très peu de la construction usitée par nos charbonniers contemporains.
Pendant des siècles, le charbon reste employé à des usages domestiques et à la préparation des métaux ; la découverte de gisements de minerais de fer importants donne un grand essor à sa fabrication : les usines métallurgiques se créent de préférence à proximité des forêts, mais, au siècle dernier l’emploi de la houille et du coke lui est funeste : il reste confiné à la cuisine, d’où bientôt il est chassé par le gaz d’éclairage, le gaz butane et l’électricité ; les gourmets le regrettent, car la cuisson au charbon de bois confère aux mets une saveur toute particulière.
Il a fallu la difficulté des temps actuels pour remettre ce combustible en faveur et lui donner une précieuse valeur.
La fabrication du « Gaz des Forêts » n’est d’ailleurs pas le seul emploi moderne du charbon de bois ; la métallurgie le recherche de nouveau, en raison de sa grande pureté, pour la préparation d’alliages spéciaux ; en outre, sa porosité le rend apte à absorber d’importantes masses de liquides ou de gaz, et cette propriété est utilisée dans le filtrage de l’eau, dans la préparation de produits pharmaceutiques ou même d’aliments destinés à la volaille ; enfin les charbons « actifs » des masques à gaz ne sont que du charbon de bois qui a subi un traitement spécial en vue de développer cette propriété d’absorber et de retenir les gaz.
Le choix des charbons pour la carbonisation
Du point de vue chimique, le bois se compose essentiellement d’environ 50 % de cellulose et de 20 à 30 % d’une matière incrustante, la lignine ; en quantités variables, on trouve aussi dans le bois, des tanins, des résines, des glucosides, des amidons, des corps gras, des matières minérales incombustibles ; ces dernières constituent les cendres lorsque le bois est détruit par combustion complète.
L’analyse du bois rigoureusement sec donne, pour cette matière pourtant complexe, une série de corps simples en proportions presque indépendantes de l’essence du bois.
Carbone | 50 % |
---|---|
Hydrogène | 6 % |
Oxygène | 42 % |
Azote | 1 % |
Cendres | 1 % |
La constitution physique du bois est connue : il est formé d’un faisceau de tubes capillaires dans lesquels circule la sève ; plus ces tubes sont fins et serrés, plus le bois est dur et lourd ; le bois de cœur, le bois de tronc sont, respectivement, plus durs et plus lourds que le bois de périphérie ou aubier et que le bois de branche.
Les essences dites dures (chêne, charme, hêtre, orme, etc ... ) sont plus lourdes que les bois tendres (peuplier, saule, bouleau, aulne, etc ... ) parce qu’elles sont constituées de vaisseaux capillaires plus fins, et plus lourdes aussi que les bois résineux (pin, sapin, mélèze, épicéa, etc ... ), dont les vaisseaux sont gonflés de résine.
Le bois qui a poussé péniblement dans un terrain aride, sec est, pour des raisons analogues, plus dur et plus lourd que le bois qui a poussé rapidement dans un terrain riche et humide.
Dans la carbonisation, la matière solide qui constitue l’enveloppe des tubes, diminue de dimension, mais conserve la forme tubulaire et le charbon de bois est poreux. Ainsi s’expliquent la facilité avec laquelle s’enflamme ce combustible et ses propriétés absorbantes vis-à-vis des liquides et des gaz.
Quelles que soient les essences carbonisées - et toutes peuvent l’être ( [1] ) - elles conservent, après carbonisation, leurs propriétés relatives, à un degré moindre, bien entendu : les essences dures donnent du charbon dur, compact, lourd ; peu poreux, ce charbon s’enflamme assez lentement, mais il est long à se réduire en cendres : son emploi dans un gazogène est économique et permet un grand rayon d’action chargement ( [2]). Au contraire, le charbon de bois tendre ou résineux, très poreux, est tendre, léger, friable : il donne un rayon d’action-chargement restreint, mais par contre, s’enflammant très vite, il donne des « reprises » plus vives que les charbons durs.
Outre les bois d’œuvre, dont la carbonisation n’est pas à envisager, l’exploitation d’une coupe fournit :
- des rondins de 7 à 15 cm. de diamètre (ou de 22 à 47 cm. de tour) et des bûches, provenant de la fente des bois de plus de 15 cm. La carbonisation de ces échantillons serait intéressante par son rendement élevé en charbon (85 à 95 kg. par stère et parfois plus), cependant, il faut songer à l’alimentation de nos foyers privés de houille et réserver les rondins comme bois de feu, leur vente à ce titre étant d’ailleurs avantageuse. Exceptionnellement, on sera conduit à les carboniser, notamment si l’accès de la coupe rend le débardage pénible et coûteux, ou si le bois est de fente difficile (chêne vert) ou encore si le bois brûle mal (châtaignier) ;
- la charbonnette, de 2 à 7 cm. de diamètre (ou de 6 à 27 cm. de tour). La charbonnette est coupée à différentes longueurs, suivant les régions : 57 cm., 66 cm. (ou 2 pieds), 80cm. ou 1m. ; les bois courts, plus droits sont d’empilage serré. Le nom donné à cet échantillon indique bien sa destination ;
- rémanents, qui comprennent les branchages de moins de 2 cm. de diamètre ; leur carbonisation est possible mais peu intéressante : les ramilles sont surtout formées d’aubier et le rendement en charbon est faible ; de plus, la proportion d’écorce est élevée et on sait que l’écorce est la partie du bois qui fournit le plus de cendres ;
4. les souches : d’extraction difficile, leur carbonisation est rarement effectuée, car il faudrait, péniblement, les débiter en morceaux et les débarrasser de la terre qui les couvre ; on n’exploite guère, pour leur résine, que les souches de résineux.
L’âge du bois a une influence sensible sur la qualité et sur le poids de charbon que l’on peut tirer d’un stère de bois ; un bois jeune contient beaucoup d’aubier : sa carbonisation a un rendement faible et donne un charbon léger, tendre, friable ; l’âge normal d’exploitation des taillis est 25 ans ; il est bien évident que les nécessités de l’heure imposeront des coupes de taillis plus jeunes, de 18 à 20 ans.
L’âge d’abattage intervient à peu près dans le même sens : le bois vert contient de 35 à 40 % de son poids d’eau ; la teneur en eau peut même atteindre 50 %, pour du bois poussé en terrain humide et abattu en pleine sève ; on conçoit que la carbonisation du bois vert oblige à brûler davantage de combustible pour vaporiser la masse d’eau ; nous y sommes cependant contraints par l’urgence qu’il y a d’entreprendre la fabrication du charbon de bois.
Il est bien préférable que le bois ait séjourné quelques mois sur le parterre des coupes jusqu’à ce que la teneur en eau soit amenée à environ 20 % : la carbonisation devient alors rémunératrice. Les bois blancs, le hêtre en rondins sont avantageusement traités après 4 à 6 mois de séchage : passé ce temps ils s’altèrent, fermentent, deviennent spongieux, perdent toute résistance, et ne peuvent donner de bon charbon ; on dit que le bois est piqué, ou chauffé, ou passé : j’ai eu à carboniser de la charbonnette de charme (excellent bois de carbonisation) mais piquée : le rendement en charbon brut a été de 55 kg.-stère ; après concassage et criblage, le rendement en bon charbon pour gazogène, a été d’environ 48 kg.-stère, ce qui est trop faible. Le hêtre fendu et les bois durs peuvent rester plus d’un an sur coupe sans se détériorer, mais il n’est pas recommandé de les y laisser plus de deux ans. Si donc le séchage du bois est nécessaire, il ne saurait être trop prolongé, tout au moins s’il se fait à l’air libre, sans une sérieuse chute de rendement. Le séchage en étuve n’est usité que dans les usines de distillation du bois, car on y dispose de grandes masses de gaz chauds et le séchage artificiel du bois permet de récupérer de grandes quantités de chaleur.
En général, l’abattage a lieu en automne et en hiver, de sorte que la carbonisation en meules se fera au printemps et en été ; l’emploi de fours métalliques permet l’opération en toutes saisons ; seule la pluie pourra empêcher le défournement ; encore, si le four est de petites dimensions, pourra-t-on le protéger à l’aide d’une bâche.
La carbonisation
Il faut bien distinguer entre la combustion et la carbonisation du bois.
Quand on chauffe un morceau de bois à l’air libre, il commence par abandonner l’eau qu’il contient : souvent on voit le bois « suer ») à l’extrémité non chauffée ; puis il émet une flamme plus ou moins chaude, plus ou moins éclairante, produite par la combustion des gaz qui se dégagent ; la flamme diminue peu à peu, la masse de bois devient incandescente, forme ce qu’on appelle la braise ; si l’air ne cesse d’arriver, la braise brûle à son tour sans flamme ou presque mais en répandant beaucoup de chaleur ; finalement, la braise disparaît en ne laissant qu’un petit amas de cendres ( [3]) avec l’oxygène de l’air ; la partie solide s’est gazéifiée, en donnant du gaz carbonique et de la vapeur d’eau.
Dans la carbonisation du bois, au contraire, on chauffe le bois à l’abri de l’air : il abandonne encore de l’eau et des gaz que l’on peut recueillir, mais on arrête le chauffage quand on a obtenu la braise qui, par refroidissement, toujours à l’abri de l’air, donne le charbon de bois.
Cette opération est comparable à une distillation, avec cette différence, toutefois que, dans une distillation, on sépare les éléments mélangés par vaporisation à des températures échelonnées sans qu’il y ait décomposition d’aucun d’eux, tandis que, sous l’action de la chaleur, certains éléments du bois se décomposent et donnent naissance à des produits nouveaux.
Le chauffage du ligneux peut être effectué sans ou avec contact avec les gaz chauds provenant d’un foyer, séparé du bois dans le premier cas, et formé dans la masse même du bois dans le second cas.
La carbonisation en vase clos (1er cas) est pratiquée dans les usines où l’on recherche surtout la récupération des produits gazeux ; elle est plus rarement pratiquée en forêt, dans des fours continus plus ou moins mobiles. Dans les meules et les fours métalliques, la carbonisation est obtenue par le deuxième procédé et les gaz émis ne sont pas récupérés.
Carbonisation en vase clos. - La figure 1 donne la disposition générale des cornues et de l’appareil de condensation des gaz et des vapeurs.
Les gaz chauds provenant d’un foyer ou d’un gazogène viennent lécher les parois d’une cornue dans laquelle on a empilé du bois ; le chauffage peut être réglé à l’aide de registres.
Les vapeurs et gaz émis par le bois se rendent dans un barillet : le tube d’amenée débouche sous le niveau de l’eau, maintenu constant par une surverse, afin de produire une pression constante dans la cornue ; de là, ils se rendent dans un condensateur à circulation d’eau puis dans un appareil à chicanes qui retient les dernières particules de goudron. Les gaz qui en sortent contiennent du gaz carbonique, de l’oxyde de carbone, un peu d’hydrogène et de carbures d’hydrogène : ils sont donc combustibles et on les envoie brûler sous des cornues en cours de distillation.
Le traitement des pyroligneux sort du cadre de cette étude : voici, d’après Klar, ce que l’on peut tirer de la carbonisation lente du hêtre en vase clos :
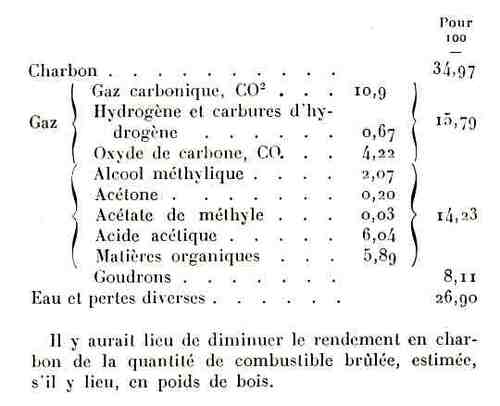
Voici ce que l’on observe aux diverses températures, au cours de la distillation :
- Jusque vers 100°-120°, le bois se dessèche sans s’altérer ;
- Jusque vers 275°-290°, le dégagement de vapeur se poursuit, le bois brunit et dans les gaz apparaissent du gaz carbonique, de l’oxyde de carbone, un peu d’acide acétique : ces corps proviennent de la décomposition des morceaux de bois voisins des parois chaudes de la cornue ;
- Vers 300° s’amorce un dégagement tumultueux de gaz, accompagné d’une forte élévation de température à l’intérieur de la cornue, sans que l’on ait besoin d’activer le foyer extérieur. C’est au cours de cette réaction exothermique que se place la formation d’une importante quantité de pyroligneux contenant de l’acide acétique, de l’alcool méthylique, de l’acétone, des goudrons, des gaz incondensables (gaz carbonique et oxyde de carbone). A partir de 350°, ces deux derniers gaz se dégagent en proportions décroissantes tandis qu’apparaissent l’hydrogène et les hydrocarbures d’hydrogène dont la proportion va sans cesse croître avec la température ;
- Entre 400° et 450°, le goudron devient épais et c’est généralement aux environs de cette dernière température qu’on cesse le chauffage. Si l’on continuait à chauffer, il se dégagerait de plus en plus d’hydrogène et d’hydrocarbures : en fermant l’appareil, ces gaz, dont la production se continue pendant quelque temps, sont réabsorbés par le charbon et le pouvoir calorifique du produit s’élève.
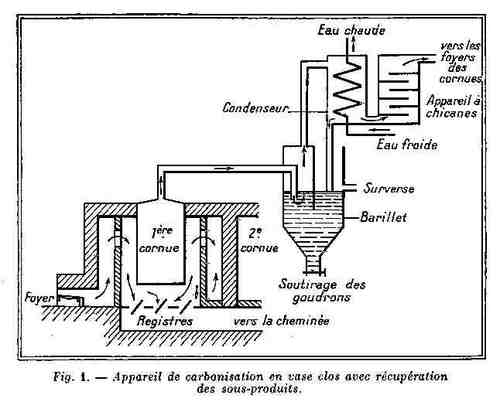
L’allure du chauffage joue un rôle important : si la température s’élève rapidement, on obtient beaucoup de gaz mais peu de distillat et de goudron ; au contraire, un chauffage lent produit moins de gaz mais plus de charbon et de pyroligneux : ce phénomène paraît devoir être attribué à la dissociation des produits distillés au contact des parois plus chaudes de la cornue.
On retiendra aussi que la température ne doit pas être trop élevée. Notamment, si l’on fait usage, en forêt, de fours métalliques, on évitera de laisser rougir les tôles : d’une part les tôles rougies se détériorent très vite, les rivures, les soudures risquent de céder ; d’autre part, le rouge cerise correspond à une température d’environ 500° et la masse incandescente intérieure est à une température notablement plus élevée : trop de gaz se dégagent qui auraient pu se réincorporer au charbon.
Carbonisation en forêt. - La carbonisation en forêt peut se faire en meules ou en fours métalliques démontables dérivés des meules ; elle peut aussi se faire en fours continus si l’on dispose d’une assez grande coupe de bois, permettant, sans augmenter les frais de transport du bois, d’alimenter les fours pendant plusieurs mois, ces appareils, démontables, étant toutefois d’un déplacement malaisé.
Meules et fours dérivés. - Quel que soit l’appareillage utilisé, meule ou four, le charbonnier doit disposer d’un certain matériel et prendre quelques précautions pour mener ses opérations à bonne fin.
a) Le petit outillage doit comprendre :
- du matériel pour le transport du bois : civière, hotte, brouette à grande roue, schlitte si le terrain se prête à son emploi ;
- des outils pour préparer le terrain : pelle, pioche, rateau , quelquefois même une faux ;
- des outils à débiter le bois : scie, serpe, hache, merlin, coins et masse ;
- une fourche à cailloux, un crible pour ramasser le charbon, un seau ; enfin il devra être approvisionné de sacs de jute, de ficelles ; une bâche lui permettra de protéger le charbon de la pluie.
b) Le faulde, ou aire sur laquelle sera édifiée la meule et le four, doit être choisi pour que l’on puisse carboniser 5 à 6 fois de suite avec du bois pris dans un rayon de 50 à 60 m. Si le terrain est accidenté, on place d’abord le faulde en bas d’une rampe et on le remonte d’une cinquantaine de m. quand les tas de bois s’éloignent par trop, ceci, afin de descendre le bois au lieu de le monter.
Le transport des bois par animaux attelés n’est intéressant que si les tas sont disséminés ou si l’on désire carboniser de grandes quantités à chaque opération.
La nature du sol influe sensiblement sur la durée et sur le rendement de la cuisson. On a vu que le bois, sous l’action de la chaleur, abandonne de la vapeur d’eau et des goudrons qui, ici, vont en grande partie s’échapper dans l’atmosphère, mais il va aussi s’en condenser à l’intérieur des appareils ; les pyroligneux s’égouttent sur le sol dans lequel ils doivent s’infiltrer : il faut donc choisir un sol sec, une terre légère, friable. On recherchera de préférence les anciens fauldes, reconnaissables à la rareté de la végétation, à la couleur noire de la terre, parsemée de débris de charbon : au cours des cuissons précédentes, la terre a subi une sorte de cuisson qui l’a rendue poreuse et apte à absorber rapidement les liquides condensés. Un sol argileux donne rarement de bons résultats aux premières opérations : les jus s’amassent en petites mares qui doivent être asséchées pour que la carbonisation progresse ; on conçoit dès lors que l’opération soit prolongée et qu’il faille brûler beaucoup de bois, ce qui affecte le rendement.
Le terrain choisi doit être débarrassé des herbes et souches qui l’encombrent, puis nivelé ; il est avantageux de le faire légèrement bombé vers le centre, surtout si le sol est argileux. Lors d’une première cuisson, on se trouvera bien de recouvrir le faulde d’une mince couche de poussier de charbon de bois.
Meules forestières, - Le charbonnier construit une cheminée au milieu du faulde, soit à l’aide de perches fichées dans le sol et reliées entre elles par des rameaux flexibles, soit en disposant de la charbonnette mince autour d’une perche centrale, de façon à former une sorte de prisme triangulaire ou carré de 10 à 15 cm. de côté. Au pied de la cheminée C (fig. 2), il place quelques broussailles ou du petit bois fendu, ou mieux des fumerons provenant d’une cuisson précédente.
Certains charbonniers établissent sur le sol une sorte de plancher de charbonnettes dirigées suivant des rayons : ces bois ne donneront que des fumerons, mais ils présentent l’avantage d’isoler la masse de bois du sol ; d’autres charbonniers empilent le bois directement sur le sol, le gros bout en bas (pour donner peu à peu l’inclinaison voulue) ; ils emploient autant que possible de la charbonnette coupée en biseau pour la première couche, afin de faciliter l’accès de l’air au foyer ; la fente va croissant du centre à la périphérie, pour éviter l’éboulement de la couverture ; les vides sont comblés de bois plus courts ; les bois crochus doivent présenter leur concavité vers l’extérieur : ils présentent ainsi moins de risques de percer la couverture lors de son effondrement.
Sur la première couche, on en dispose d’autres de diamètres plus faibles ; leur nombre dépend du volume que l’on veut donner à la meule. La dernière couche est posée presque à plat, et l’édifice ressemble, grossièrement, à un paraboloïde de révolution. Si D est le diamètre de base et II la hauteur totale, toutes deux exprimées en mètres, le volume de bois empilé est à peu près égal, en stères, au nombre donné par la formule :
$$$ V = \frac{\pi D^{2}}{4} \times \frac{H}{2}$$$
En France, le volume des meules varie de 8 à 15 stères, mais nous en avons vu qui atteignaient 30 à 40 stères dans le Centre et 140 stères en Provence.
L’édifice de bois est couvert d’abord d’une couche de 7 à 8 cm. de foin, paille, feuilles, mousse ou gazon puis d’une couche de 8 à 10 cm. de terre légère : l’ensemble doit être étanche et empêcher tous accès d’air autres que ceux prévus par le charbonnier : la cheminée n’est pas bouchée, et au pied de la meule, l’ouvrier ménage des évents E pour l’admission d’air.
Pour allumer, le charbonnier enlève la perche centrale, verse dans la cheminée quelques pelles de braise rougec, puis alimente le foyer ainsi créé avec du bois fendu ; J’alimentation doit se faire à plusieurs reprises et chaque fois, l’ouvrier doit faire descendre le bois avec la perche, sinon le foyer n’étant pas assez important pour que le bois commence à s’effondrer, il se forme une voûte et la distillation ne pouvant s’amorcer, la meule s’éteint.
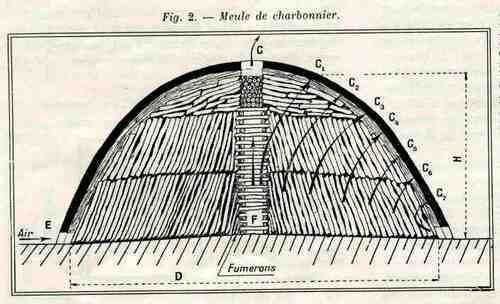
Les gaz de combustion, chauds, s’élèvent et ce mouvement crée un appel d’air par les évents, le foyer F se développe et la fumée sort en abondance : les gaz chauds, dépourvus d’oxygène, lèchent le bois qui avoisine la cheminée ; ce bois sèche et distille à l’abri de l’air ; la fumée sort d’abord blanche (vapeur d’eau condensée) puis jaune foncé (vapeurs de goudron) quand, la température de 300° étant atteinte, la réaction exothermique se déclenche ; finalement la fumée s’éclaircit, devient légère, bleutée : à ce signe, le charbonnier reconnaît qu’il est temps de fermer la cheminée centrale C, puis d’ouvrir toute une série de nouvelles cheminées C1 disposées autour de la première, sur un même plan horizontal : les gaz, ne trouvant d’autres issues, suivent un trajet différent et une nouvelle masse de bois distille, émettant des fumées successivement blanches, jaunes, bleutées, après quoi le charbonnier bouche les cheminées C1 pour en ouvrir d’autres C2 un peu plus bas, et ainsi de suite. Les flèches indiquent approximativement les trajets successifs des gaz chauds. Lorsque les dernières cheminées, telles que C7 ont cessé de fumer, on les bouche ainsi que les évents et la masse incandescente s’éteint et se refroidit peu à peu.
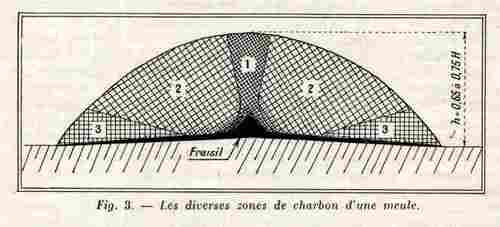
Le démoulage, après refroidissement d’une durée variable suivant l’importance de la meule, s’opère le plus souvent de nuit, afin de rendre plus visibles les joints encore incandescents. La terre est enlevée avec précaution, au râteau, en commençant par le haut ; on découvre peu à peu la couche végétale, qui n’est pas, en général détruite, mais engluée de goudron : on l’enlève par plaques, et un ouvrier adroit peut fort bien éviter la chute de terre dans le charbon ; celui-ci est ramassé à la fourche à cailloux ; on élimine les larges lambeaux d’écorce détachés des rondins, ainsi que les fumerons qui ne se cassent pas au choc ou présentent une cassure marron foncé ; les débris qui passent à travers les dents de la fourche sont tamisés.
Critique de la meule. - Au cours de la cuisson, la meule s’affaisse de 1/3 à 1/4 de la hauteur primitive : le bois, en carbonisant, se contracte et l’enveloppe de terre descend ; l’ouvrier doit surveiller la meule d’une façon constante et boucher les fissures qui se produisent.
L’allure de la carbonisation n’est pas aussi régulière qu’il est dit plus haut ; le vent active le feu du côté qu’il frappe : pour que la meule s’affaisse régulièrement, le charbonnier doit boucher plus ou moins les évents et les cheminées et parfois tendre des toiles en guise de paravent. La pluie détrempe la meule et gêne le développement de la cuisson.
La meule exige donc la présence continue et attentive de l’ouvrier qui doit posséder une grande science du métier : on ne s’improvise pas charbonnier de meule, on le devient après un long apprentissage.
Mais il est un autre inconvénient, plus grave à mon avis, que je veux signaler, et qui tient au fonctionnement même de la meule : la carbonisation progresse à la manière d’une fleur qui s’épanouit ; la partie qui a voisine la cheminée (région 1 , fig3) a subi longtemps l’action des gaz chauds et donne un charbon un peu trop cuit, comparable à la braise de boulanger, léger, friable, mais cependant très acceptable pour le gazogène. Le charbon de la région 2 a été cuit moins longtemps, à température sensiblement régulière et convient parfaitement à l’alimentation des gazogènes. Mais au fur et à mesure qu’on s’approche de la périphérie (région 3), le bois a cuit de plus en plus lentement, à basse température, de sorte qu’il est mal dégoudronné. Ce charbon est supporté difficilement par les gazogènes à tuyère (de même d’ailleurs que le charbon humide). Naturellement, les zones ne sont pas aussi nettement tranchées que la figure 3 semble l’indiquer.

Dans ces gazogènes (fig. 4), le foyer est assez restreint : nous avons représenté son contour approximatif par un trait pointillé. Le charbon, au voisinage de ce foyer à haute température, achève de distiller, mais comme les goudrons le traversent rapidement, parfois sur un faible parcours (voir flèches, fig. 4), le temps fait défaut pour leur destruction totale et les gaz, à la sortie du gazogène en contiennent encore. Ces goudrons se condensent dans le refroidisseur, se déposent sur les filtres en toile qui sont colmatés. Si on limite le refroidissement avant les toiles, pour le pousser après, les condensations se produisent à l’entrée du moteur, les soupapes collent et les bougies s’encrassent.
On conçoit donc que le charbon de meule, non homogène, convienne mal à l’alimentation des gazogènes. Exceptionnellement, on pourrait l’utiliser, à défaut d’autre, mais le mieux serait de convaincre les charbonniers de réserver le charbon de périphérie pour les besoins domestiques et de ne donner aux usagers du gazogène que le charbon prélevé à l’intérieur d’un cône à axe vertical et qui aurait comme ouverture un angle d’environ 120°.
Vous dirai-je que, si j’ai réussi à convaincre quelques charbonniers, il y en a beaucoup sur lesquels je n’ai eu aucune influence ? C’est que, chez les charbonniers, on est fier du métier, on a l’orgueil du produit bien fait - et l’on a raison : c’est une des rares corporations où, chez tous les individus sans exception, on trouve la plus haute expression de la conscience professionnelle. Malheureusernent, la vie à l’écart des centres habités rend le charbonnier moins compréhensif aux choses nouvelles et il a peine à comprendre les exigences des moteurs et des gazogènes.
Fours métalliques dérivés des meules. - Les constructeurs de fours métalliques démontables se sont proposé : 1° de remplacer le revêtement terreux de la meule par une enveloppe de tôle, en vue d’éviter le mélange de terre et de charbon ; 2° de provoquer une circulation rationnelle des gaz chauds dans le but de rendre la carbonisation plus rapide et d’obtenir un produit plus homogène. Enfin ils se sont préoccupés de construire des appareils faciles à démonter et à transporter, tout en permettant de traiter une masse importante de bois.
Dans ce domaine comme dans celui des gazogènes, les déboires du début furent nombreux, et il faut rendre hommage aux constructeurs qui, comme Delhommeau, Trihan , Forïndust, Magnien se sont acharnés : leurs efforts ont été couronnés de succès, leurs réalisations sont des modèles et les fours nouveaux qui apparaissent actuellement sur le marché sont le plus souvent des adaptations, des améliorations plus ou moins heureuses.
Dans la pratique, les fours métalliques se sont révé lés plus avantageux qu’il n’avait été prévu :
- ils réduisent la durée de l’apprentissage des charbonniers : en quelques jours, l’apprenti connaît le maniement des appareils et en quelques semaines, il devient un préparateur capable de produire un excellent charbon et de gagner suffisamment sa vie ;
- l’empilage des bois est plus commode et plus rapide ; la surveillance est réduite au minimum, ce qui autorise une organisation industrielle rémunératrice des chantiers, avec une durée normale de présence diurne des ouvriers ; le travail nocturne est exceptionnel et n’intervient guère qu’au début d’une coupe, alors que le personnel ne connaît pas encore le comportement du bois au feu.
- la production est presque soustraite à l’influence des intempéries ; un grand vent exige cependant une surveillance un peu plus attentive et la pluie peut empêcher le défournement.
En vue du démontage et du transport des fours, il est désirable que les appareils soient composés d’un petit nombre de grosses pièces légères.
Deux modes de construction sont employés : les fours contenant jusqu’à 8 stères sont en général constitués par des viroles superposées ; la virole inférieure repose soit directement sur le sol, soit sur un socle annulaire creux, soit encore sur des rondins. La virole supérieure supporte le couvercle ; les fours de capacité plus grande sont composés de panneaux plans ou cintrés ; l’ensemble présente alors la forme d’un cylindre ou d’un prisme à base polygonale réguIière. Celle dernière conformation est sans influence sur la cuisson, si les évents, à la base du four sont bien répartis ; ce que l’on peut craindre, avec des fours à faces planes, c’est la déformation des tôles, aussi sont-elecs le plus souvent raidies par des cornières ou des nervures.
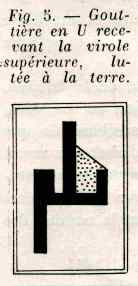
Les viroles sont en tôle mince de 2 à 3 mm. pour les pièces exposées au feu et en tôle de 1,5 mm à 2 mm, pour les éléments supérieurs ; les panneaux sont découpés dans des tôles de 2 à 3 mm., les différentes parties d’un même élément sont assemblées par rivets ou par soudure (joints ou bandes, ou continue) ; la soudure continue est bien préférable : elle est plus étanche et supporte mieux la dilatation sous l’effet de la chaleur.
Il est indispensable que les joints entre deux éléments soient parfaitement étanches, sinon l’extinction du feu devient impossible. Dans le premier mode de construction, une virole repose dans une gouttière en forme d’U soudée sur la virole inférieure (fig. 5) ; il suffit de tasser dans la gouttière un peu de terre légère pour assurer une bonne étanchéité : les goudrons qui traversent la terre colmatent les interstices ; cependant on devra débarrasser la terre des cailloux et des racines qu’elle contient : les racines surtout sont à éliminer, car en se calcinant, elles laissent passage à un mince filet d’air qui entretient le feu.
Les joints verticaux sont plus difficiles à exécuter ; les bords relevés des éléments enserrent une tresse d’amiante et sont maintenus serrés l’un contre l’autre par des pinces ; ou bien, les bords s’emboîtent pour former une sorte de canal vertical dans lequel on tasse du sable ou de la terre légère ; les tôles sont maintenues serrées l’une contre l’autre soit par un clavetage, soit à l’aide de boulons (fig. 6). La terre argileuse est à éviter dans la confection du joint : en cuisant, elle se contracte et présente des fissures larges que le goudron narrive pas à colmater ; de plus, pendant la carbonisation, les tôles se dilatent et serrent le joint, mais, pendant le refroidissement, les tôles se contractent et le joint est soulagé, au moment précisément où il devrait être comprimé : il faut qu’à ce moment la matière employée puisse s’écouler par gravitation et faire obstacle aux entrées d’air, d’où le choix d’une matière pulvérulente.
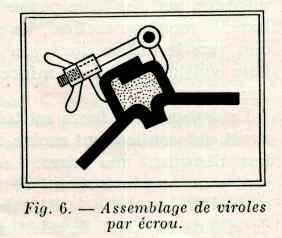
Le couvercle doit être suffisamment raidi pour pouvoir supporter, sans se déformer, le poids d’un homme au moment de l’allumage : il est en général rendu rigide par des cornières soudées ou par des rainures obtenues il la roulette.
En règle générale, la base du four présente des ouvertures ou évents réglables permettant d’agir sur l’admission d’air, et le couvercle présente en son centre une ouverture pour l’allumage. La cheminée d’allumage se construit comme celle d’une meule, à l’aide de charbonnette placée soit autour d’une perche qu’on enlève pour verser des charbons ardents, soit autour d’un tuyau en tôle mince qui facilite la chute de la braise rouge et qu’on enlève dès que le feu est pris.
L’empilage du bois peut se faire de diverses façons : soit en dressant toutes les couches verticalement, soit en mettant tous les bois à plat, soit encore en alternant les couches verticales et horizontales : dans ce dernier cas, la première couche sera de préférence verticale, car une couche horizontale gênerait le passage de l’air vers le foyer.
Nous ne pensons pas nécessaire de raccourcir les bois, et préférons les employer suivant les longueurs consacrées par les usages locaux ; sans doute, avec des bois courts et des bois longs mélangés on remplit mieux les vides, mais la légère augmentation de production par fournée ne compense pas le supplément de travail. Les rondins peuvent être carbonisés jusqu’à 15 cm. de diamètre : au delà il faut soit les refendre, soit les faire passer deux fois dans le four. Dans le montage vertical, les grosses bûches sont placées vers le milieu du rayon du four ; on évitera de faire voisiner des bois minces avec des échantillons très gros.
La capacité des fours est très variable : on en construit qui contiennent moins de 1/2 stère, mais d’autres atteignent 100 stères. Les fours de 4 à 8 stères sont d’un emploi courant en forêt, en raison de leur maniabilité et de la facilité de leur service. La durée de la cuisson, pour de tels fours, varie de 16 à 24 h. On allume de façon que la période calme de la distillation se déroule la nuit sans surveillance, la fin de la carbonisation demandant seule quelque attention.
L’allumage effectué et le foyer ayant été suffisamment alimenté avec du petit bois versé dans la cheminée, on règle les évents : peu ouverts du côté du vent, on les ouvre davantage du côté opposé ; les évents seront plus largement ouverts pour traiter des gros bois verts que lorsqu’on opère sur des échantillons minces ou sur des bois secs ou tendres, ou résineux, ou encore piqués. Lorsqu’on commence un chantier, nous recommandons de faire du feu avec un peu de ce bois à traiter et d’observer son comporte ment au feu : si la braise est dure, longue à tomber en cendres, on peut marcher à une allure assez vive (évents très ouverts) ; si au contraire la braise disparaît rapidement, on doit conduire l’opération lentement.
La carbonisation est toujours plus avancée du côté frappé par le vent : on ferme les évents en se guidant sur la fumée qui sort des cheminées (elle est légèrement bleutée quand la cuisson est complète) et par l’aspect du feu visible par les évents : la fin de la carbonisation est annoncée au voisinage d’une prise d’air par la disparition des flammes et par la présence de braise bien rouge ; si la braise se couvre de cendres blanches, c’est que la carbonisation a été trop poussée dans cette région et au démontage il y aura peu de charbon en ce point. Surtout on évitera de laisser rougir les tôles, ainsi que nous l’avons dit en étudiant la distillation en vase clos.
Lorsque tous les évents sont fermés, au besoin en les recouvrant de terre, on vérifie que tous les joints sont en bon état. L’extinction des fours de 4 à 8 stères demande de 15 à 24 h.
Un four formé d’anneaux doit être complètement démonté pour le démoulage ; au contraire, avec les fours à panneaux, il suffit d’ouvrir l’une des faces, et ceci permet de récolter le charbon même par temps de pluie.
Deuxième partie - La Nature N° 3065 - 15 janvier 1941
Quelques types de four
Les constructeurs se sont préoccupés d’assurer une circulation rationnelle des gaz dans la masse de bois : ils se sont, en général, efforcés de les diriger vers la périphérie de l’édifice ligneux, pour sécher les bois qui y sont empilés et accélérer leur carbonisation, qui, clans la meule, est lente.
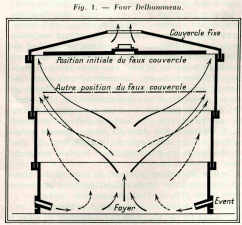
Voici par exemple, le four Delhommeau (fig. 1) : il se compose de trois viroles superposées ; la virole inférieure présente une série d’ouvertures pour l’accès de l’air ; lorsque le bois est empilé, on place, directement sur les bûches, un plafond mobile dont le diamètre est inférieur de quelques cm. au diamètre intérieur des viroles ; on dispose ensuite le couvercle fixe qui est supporté par la gouttière de la virole supérieure ; ces deux couvercles sont percés d’un trou central pour l’allumage. Lorsque le feu est bien pris, que la fumée se dégage abondamment, on ferme l’ouverture du plafond mobile : les gaz chauds du foyer sont alors obligés de suivre le trajet indiqué par les flèches en trait plein ; au fur et à mesure de l’effondrement des bois, le plafond mobile descend et les gaz suivent des trajets analogues à celui indiqué en trait pointillé.
On reconnaît la fin de la carbonisation à l’aspect des évents (braise rouge, pas de flamme) et aussi à la position atteinte par le plafond, position que l’on peut repérer par des lumières, normalement fermées, pratiquées sur le plafond. On ferme peu à peu tous les évents, selon l’avancement de la cuisson ; un petit talus en terre légère suffit à rendre la fermeture étanche.
Remarquons que le plafond mobile régularise l’allure générale de la distillation : lorsque le foyer s’active d’un côté (vent ou ouvertures mal réglées) le bord du plafond descend plus bas de ce côté, le passage des gaz devient plus grand à l’opposé et la carbonisation s’active dans cette région ; peu à peu le plafond redevient horizontal puis s’incline en sens inverse et reprend finalement une position correcte.
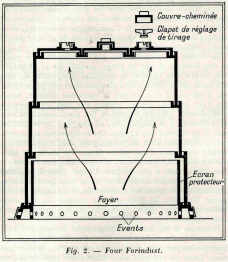
Le four Forindust (fig. 2) comprend trois éléments cylindriques superposés reposant sur un socle creux formé d’un certain nombre de secteurs emboîtés de façon à réaliser un joint cylindrique vertical de faible hauteur facile à rendre étanche. Les évents sont munis de volets de réglage. Le couvercle est en trois pièces. Il comporte une cheminée centrale pour l’allumage, que l’on ferme quand le feu est allumé, et six cheminées réparties régulièrement à la périphérie. Ces dernières peuvent être plus ou moins obstruées par des clapets que l’on suspend soit sur le rebord de la cheminée, soit dans des fentes plus ou moins profondes de ce même rebord. La répartition des cheminées oblige les gaz à traverser toute la masse de bois.
Le four Magnein est composé de deux viroles tron-coniques ou d’une virole cylindrique et d’une autre tronconique (fig. 3), et d’un couvercle rigide.
La virole inférieure repose sur 8 rondins de 1 m. de long et de 10 cm. de diamètre disposés en étoile ; les extrémités intérieures ne doivent pas se toucher et les extrémités extérieures doivent sortir d’environ 10 cm. de la virole. Au centre du faulde, le charbonnier monte une cheminée en charbonnette et établit sur les rondins un caillebotis de brins minces destiné à isoler l’édifice ligneux du sol ; lorsque la charbonnette est coupée à 66 cm., il est nécessaire de disposer entre les rondins de l’étoile, d’autres plus courts, ne débouchant pas de la virole mais ne touchant pas les autres rondins. La première virole est emplie de bois placé soit verticalement, soit horizontalement : la deuxième virole est placée sur la première et on achève l’empilage en ménageant toujours la cheminée centrale. Le couvercle est alors mis en place et les gouttières sont remplies de terre légère. Entre les rondins, on engage sous la virole et le caillebotis 8 coudes : les uns que nous appellerons coudes-cheminées, au nombre de quatre, comportent un tuyau de même hauteur que le four ; ils sont installés aux extrémités de deux diamètres perpendiculaires ; les quatre autres coudes, plus courts, que nous nommerons coudes-évents sont intercalés entre les précédents ; un petit talus de terre à la base du four couvre l’espace libre entre la virole et le sol. Les coudes-évents peuvent être supprimés : il suffit de tasser légèrement la terre du talus et de faire des trous avec un rondin taillé en pointe (fig. 9).
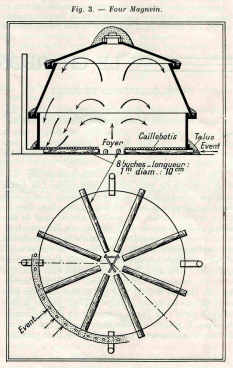
L’allumage se fait en versant dans la cheminée, par le trou central du plafond, deux ou trois pelletées de braise rouge ; on alimente le foyer à plusieurs reprises avec du petit bois et on obture la cheminée centrale avec un petit couvercle, quand la fumée sort abondamment ; on confectionne son joint avec de la terre.
L’air entre par les évents et accède au foyer par le canal limité par le sol, deux rondins voisins et le caillebotis, qui d’ailleurs laisse passer un peu d’air ; au foyer l’oxygène brûle une partie du bois et les gaz chauds (gaz carbonique, azote, vapeur d’eau, pyroligneux) s’élèvent dans la cheminée ; ils sont rabattus vers le bas par le couvercle et l’enveloppe et ne trouvent d’autres issues que les coudes-cheminées qui se mettent à fumer : la totalité de la masse de bois est baignée par les gaz chauds. Une heure environ après l’allumage, la fumée sort tumultueusement des cheminées ; d’abord blanche, elle vire peu à peu au jaune foncé et devient légèrement bleutée à la fin de la carbonisation. Parfois, la fumée sort également par les évents : un coup de vent a activé le foyer, la fumée s’est formée en abondance, la pression a augmenté et forcé les gaz à refluer par les évents ; l’entrée d’air est interrompue et l’influence du coup de vent est freinée.
Il est avantageux d’allumer le four vers 16 ou 17 h. : on réserve ainsi la période calme du séchage pour la nuit et on se dispense de surveillance nocturne.
La fin de la carbonisation, le lendemain matin, demande de l’attention. Si les cheminées ne fument plus, le foyer est éteint, soit parce que, la veille, on a confectionné trop tôt le talus au bas du four, soit parce que le foyer n’a pas été assez alimenté, soit encore que les bois ne se sont pas effondrés : il faut alors dégager le pied du four, allumer de nouveau et alimenter copieusement le foyer. Si les cheminées ne fument pas abondamment, on peut se contenter de dégager le pied du four pour activer le foyer : ceci se produit souvent avec de gros bois ou avec du bois vert ; il faut éviter la sortie de flammes par 1es évents, car ce signe dénote une combustion trop active que l’on peut freiner en fermant plus ou moins les entrées d’air.
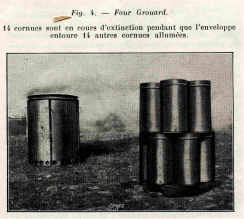
La cuisson est terminée en un point quand, par le trou correspondant on ne voit que de la braise rouge, sans flamme ; de plus, si, avec un rondin courbe passé dans le trou , on fait levier pour soulever le caillebotis, celui-ci doit s’effondrer sans effort : on peut alors boucher le trou ; la fermeture des évents s’effectue d’abord du côté frappé par le vent ; lorsqu’on a bouché les trous voisins d’une cheminée, celle-ci peut être enlevée et remise en place, quand elle est froide, sur la face opposée au vent.
Lorsque tous les tuyaux sont enlevés, on reforme le talus en le tassant légèrement et on visite les joints : l’extinction commence et elle durera de 15 à 18 h., si le four est bien étanche.
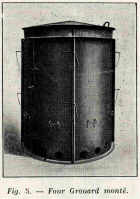
Fours à chauffage extérieur sans récupération. - Ces fours se rapprochent des cornues de distillation par le chauffage extérieur, et des fours métalliques à foyers intérieurs, par l’échappement libre des fumées. Dans celte catégorie, nous citerons le four Grouard frères (fig. 4 et 5) : ce four cornprend 14 cuves d’une capacité totale de 2 stères ; chaque cuve, garnie de bois, reçoit un couvercle non étanche ; sur un socle métallique on place 7 cuves (une au centre, six autour de la première), puis au-dessus les sept autres cuves. Les intervalles sont remplis de bois d’allumage. Une enveloppe circulaire en panneaux assemblés par clavettes, entoure les cornues ; elle est surmontée d’un couvercle mobile en hauteur afin de régler le tirage. L’allumage se fait avec du petit bois, par celui des évents de l’enveloppe tourné vers le vent. Lorsque le feu est bien allumé, on abaisse le couvercle : les flammes du foyer lèchent les parois des cuves ; le bois commence à sécher puis il distille : les gaz qui s’échappent par le couvercle non étanche des cuves s’enflamment : si le foyer extérieur est suffisamment vif, la période de réactions exothermiques se déclenche et la carbonisation continue, même lorsque le bois extérieur est réduit en cendres. L’opération, de l’allumage à la fin de la distillation, dure de 4 h. 1/2 à 5 h. On enlève l’enveloppe lorsque le four n’émet plus de fumée. Il est intéressant de disposer de deux jeux de cuves pour une enveloppe extérieure.
Fours continus. - Dans les fours continus, on se propose de réaliser à intervalles réguliers l’extraction du charbon de bois et l’alimentation en bois. D’une manière générale, on peut leur reprocher : un prix d’achat élevé, l’emploi d’une main-d’œuvre diurne et nocturne toujours onéreuse, une mobilité restreinte obligeant à débarder le bois, le débit du bois en petits morceaux alors qu’il est plus facile de casser le charbon. Par contre, la production est régulière, le rendement en charbon élevé, du fait que l’on peut récupérer les gaz de distillation pour le chauffage du four, ainsi qu’une importante fraction des pyroligneux ; enfin, le charbon obtenu est homogène et propre ; au surplus, si l’on peut disposer d’une batterie de fours, la manutention peut être rendue mécanique et le personnel est alors assez réduit.
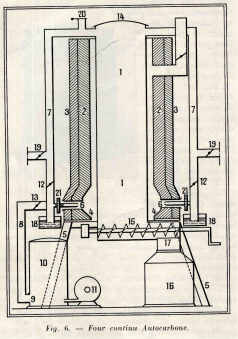
Voici, dans cette catégorie le four Autocarbone (fig. 6) : il est constitué par une cornue (1) entourée d’une enveloppe réfractaire (2) calorifugée (3), à la base de laquelle est ménagée une chambre de chauffe (4), le tout reposant sur un pied-support (5). Des brûleurs à gaz (6), peuvent être alimentés en marche normale par les gaz de distillation (tuyauterie 7), à l’allumage par un gazogène (10) à air pulsé (soufflerie 11), à l’aide de la tuyauterie (8) ; le changement d’alimentation des brûleurs s’obtient par la manœuvre des vannes 12 et 13 ; les disques (21) permettent de régler la température du foyer.
Le chargement se fait par la porte étanche (14), l’extraction à l’aide de la vis d’Archimède (15) et la vanne (17). Le charbon incandescent est recueilli dans l’étouffoir (16).
Les bacs à niveau constant (18) régularisent la pression.
Initialement, la partie inférieure est remplie de charbon jusqu’à hauteur des brûleurs, puis de bois découpé en petits morceaux. La porte supérieure étant fermée, on place un étouffoir à la base de L’extracteur, on ouvre la soupape d’échappement (20), on allume le gazogène, puis les brûleurs. Peu après, la vapeur commence à sortir par la soupape ; après environ 2 h. de marche la vapeur commence à se colorer en jaune : le séchage étant terminé, la distillation commence : quand la proportion de gaz combustible est suffisante, on ferme la soupape 20 et on ouvre les vannes 12, puis on ferme progressivement la vanne 13 : la soufflerie est alors arrêtée. L’extraction peut être continue (commande de la vis 15 au moteur) ou intermittente (commande manuelle) ; selon l’importance de la cornue et de l’étouffoir, celui-ci est remplacé par un récipient vide au bout d’un temps variable de 1/2 h. à 1 h. Le chargement peut être continu ou discontinu.
La pression du gaz varie de 100 à 200 mm. d’eau ; lorsque les gaz sont produits en quantité supérieure aux besoins des brûleurs, la pression monte et les vannes 19 permettent de la maintenir constante en évacuant les gaz dans d’autres appareils d’utilisation, par exemple dans des moteurs auxiliaires (éclairage, débit du bois, concassage du charbon).
Il est possible de recueillir les produits condensables en faisant passer les gaz dans des appareils de récupération appropriés.
Fours à bain métallique. - Dans ces fours, d’invention récente, le bois débité en petits morceaux est plongé dans un bain métallique dans lequel il subit les phases successives de la carbonisation. La température de fusion du métal doit être supérieure à 300° pour que les réactions exothermiques puissent se déclencher, et la tension superficielle du bain doit être telle que le métal ne pénètre pas par capillarité dans les pores du charbon et que, dès la sortie du bain, le charbon ne contienne aucune trace de métal : le plomb répond à ces conditions ; sa température de fusion est 327°.
L’appareil Hereng est une sorte de cornue horizontale dont la sole est constituée par un bain de plomb fondu ; le combustible déversé dans une trémie avance le long d’un séchoir dont le chauffage est assuré par une circulation de gaz chauds provenant du four : il perd son humidité ainsi qu’un peu d’air et d’anhydride carbonique ; une chaîne convoyeuse l’entraîne vers le bain de plomb : placé à la partie supérieure de la chaîne, le bois subit un commencement de distillation avant son immersion, assurée par des dalles de fonte solidaires des maillons de la chaîne.
Le charbon entraîné dans le bain à la fois par un propulseur et par le courant que l’on imprime au métal en fusion est dirigé vers un extracteur qui le précipite, après égouttage, dans un étouffoir.
La température à l’entrée ne dépasse pas 360° : la température finale est réglée suivant le résultat que l’on veut obtenir. La chaleur nécessaire est fournie par une circulation de gaz dans des tuyaux qui traversent la sole ; ces gaz peuvent être ceux qui proviennent de la distillation.
Ce four permet le traitement de tous les déchets végétaux ; on peut arrêter la distillation et la reprendre en quelques minutes ; le bois étant complètement immergé, les opérations se déroulent rapidement, sans surchauffe, avec un excellent rendement ; l’étanchéité parfaite des parois métalliques permet de recueillir le maximum de produits de distillation.
Nous avons comparé déjà le charbon de meule et le charbon de fours démontables. Le charbon provenant de la distillation en vase clos et le charbon de fours continus d’une part, le charbon de fours à échappement libre des fumées d’autre part ont des valeurs à peu près équivalentes ; cependant le premier est généralement plus léger et plus friable.
La fabrication en fours est peu économique car elle laisse partir en fumée des produits de haute valeur.
Cependant c’est le mode le plus répandu actuellement en France. C’est qu’en effet, la pénurie d’essence a imposé l’obtention rapide de tonnages importants de charbon de bois et que les fours pouvaient être plus rapidement construits que les fours dits à récupération. C’est donc avec juste raison que l’Administration des Eaux et Forêts a mis en commande un nombre imposant de fours (40000). Son choix s’est judicieusement porté sur l’un des plus rustiques, des plus maniables et des moins coûteux. Sa capacité est de 4stères à 4 stères 5. Sa durée est assez longue (deux ans à deux ans et demi) pour que l’amortissement ne grève pas trop le prix de revient du charbon. Constitué d’un petit nombre de pièces en tôle mince (1,5 et 2 mm), sa fabrication est très rapide : au 10 novembre 6 000 fours avaient été livrés et la cadence des livraisons s’est accélérée de plus en plus. Ces fours sont loués à des particuliers à des conditions très avantageuses et le prix de location ne fait cependant pas obstacle aux fabrications d’autres modèles.
La durée de ces fours permettra à l’industrie de développer la construction de fours à récupération et d’usines pour le traitement des produits récupérés. Il semble bien d’ailleurs que l’opinion des milieux intéressés s’oriente dans ce sens. Cependant, nous pensons que les fours à échappement libre ne disparaîtront pas complètement, et que l’on continuera à les employer, notamment dans les régions peu accessibles, où le débardage des bois est difficile.
Troisième partie, La Nature N° 3066 - 15 février 1941
Préparation du charbon de bois pour gazogènes. - Dans la préparation du charbon de bois pour gazogènes, on devra observer les prescriptions de l’Arrêté du 14 septembre 1940 ( [4]) que nous reproduisons ci-après :
Article premier. - Le charbon de bois pour gazogènes destinés à la traction automobile sera vendu sous l’une des dénominations suivantes, à l’exclusion de toute autre :
- Charbon de bois n°1 pour gazogènes ;
- Charbon n° 2 pour gazogènes.
Art. 2. - Le charbon de bois n°1 est un mélange de morceaux dont les dimensions sont comprises entre 8 et 30 mm. Le charbon de bois n° 2 est un mélange de morceaux dont les dimensions sont comprises entre 25 et 70 mm.
Art. 3. - Les deux produits précédents devront répondre, en outre, au moment de leur vente au consommateur, aux caractéristiques générales suivantes :
Taux d’humidité maximum : 8 % en poids ;
Teneur en cendres maximum : 5 % en poids ;
Ils ne devront pas contenir plus de 3 % en poids de poussières et de particules de dimensions inférieures à celles fixées ci-dessus, ni aucun morceau incomplètement carbonisé, ni aucun corps étranger tel que terre, pierres, particules métalliques, etc ...
Art. 4. - Le charbon de bois sera livré en emballages étanches à l’humidité atmosphérique, d’une contenance de 50 à 60 I. (8 à 15 kg. de charbon), de section carrée ou circulaire, ayant environ 30 cm. de côté ou de diamètre.
Ces emballages porteront les indications suivantes, à l’exclusion de toute autre.
- Dénomination du produit, conformément à l’article premier ;
- Poids net du combustible ramené au kg. immédiatement inférieur.
Art. 5. - Le produit sera vendu exclusivement au poids, d’après le nombre de kg. indiqué sur les emballages.
Nous allons examiner pourquoi ces prescriptions ont été édictées et comment on peut s’y conformer.
Impuretés et imbrûlés. - La terre, les pierres, les particules métalliques ( [5]) doivent être éliminés en raison de la dureté des mâchefers que ces impuretés formeraient dans les foyers des gazogènes : c’est au ramassage du charbon que l’on risque de les introduire ; cette opération se fera avec une fourche dont les dents sont espacées d’environ 3 cm., et non à la pelle ; les derniers débris seront criblés et triés.
Au cours du ramassage on éliminera les lambeaux d’écorce qui souvent sont détachés des rondins, car on a vu que l’écorce apporte beaucoup de cendres.
On rejettera également les imbrûlés, c’est-à-dire les parties qui ne se cassent pas au choc ou qui présentent une cassure marron, et aussi les bois vernissés de goudron.
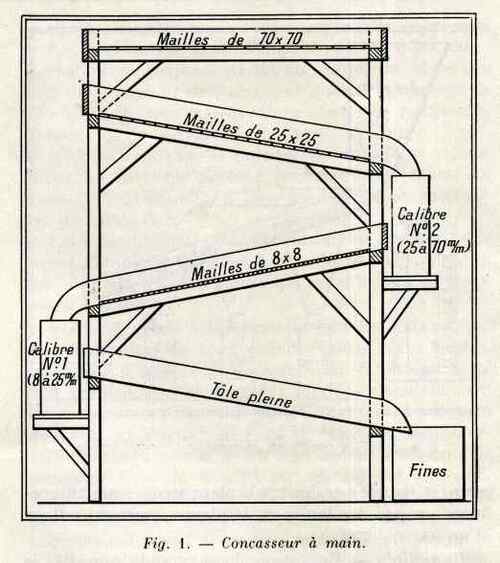
Concassage, calibrage, dépoussiérage. - On conçoit que le charbon tiré du four ou de la cornue doive être concassé : les gros morceaux arrêtant, dans le gazogène, la descente régulière de la masse en réserve dans la trémie, il se formerait des « voûtes » au-dessus du foyer et la production du gaz serait ralentie, parfois même arrêtée, jusqu’au moment où une secousse du véhicule briserait la voûte. D’autre part, le combustible ne doit être ni trop fin, ni trop gros : trop fin, il ne laisse pas passer l’air en assez grande quantité, trop gros, il le laisse passer trop facilement ; dans l’un comme dans l’autre cas, la production du gaz est insuffisante ; on admet donc aisément la nécessité de fixer des dimensions maxima et minima ; l’arrêté du 14 septembre prévoit deux calibres consacrés par l’usage : nous expliquerons, dans un prochain article, la nécessité de deux calibres et de deux seulement.
Généralement, la même machine exécute le concas sage, le calibrage, le dépoussiérage et l’ensachage. Voici tout d’abord une installation rustique facile à construire et qui convient très bien aux petites exploitations : une charpente (fig. 1) composée de 4 pieds et de traverses, supporte une table de cassage horizontale formée d’un treillis à mailles de 70 mm. que l’on peut fabriquer avec du fil d’acier ; en dessous sont placés successivement un tamis métallique à mailles de 25 à 30 mm. qui retient le charbon n° 2 et le dirige vers un sac, puis une toile à mailles de 8 mm. qui fournit le calibre n° 1 et enfin une tôle pleine qui recueille les poussiers. Les casseurs doivent stationner sur une planche fixée à une certaine hauteur ; ils cassent le charbon avec un rondin ou un petit maillet ; ils doivent aider le charbon à descendre vers les sacs car la pente des tamis ne peut être très forte, sinon la proportion de menu augmente ; cet appareil doit, sauf cas de mauvais temps, être installé à l’air libre pour que la poussière soit entraînée par le vent.
Les grandes entreprises emploieront avantageusement des concasseurs entraînés par un moteur ; le dispositif de concassage proprement dit doit casser le charbon par choc et non pas l’écraser ; ce dispositif est constitué :
- soit par un cylindre garni de doigts montés en hélice (système Delhommeau, fig. 2) et passant entre les dents d’un peigne placé au fond d’une trémie ;
- soit par deux cylindres tournant en sens inverse : ces cylindres portent des couronnes de dents pointues, les couronnes de l’un des cylindres alternant avec les couronnes de l’autre (système Rolland ou Vélard, fig. 3).
Dans l’un comme dans l’autre cas, on peut régler la grosseur des morceaux par la suppression de doigts au cylindre et au peigne (1er cas) ou par l’écartement des cylindres (2e cas).
Les poussières sont parfois aspirées par un ventilateur dont l’ouïe est raccordée à la trémie au-dessous du casseur. La classification des morceaux par grosseur est assurée par des tamis plans secoués mécanique ment ou par des tamis en tambours tournant autour d’un axe oblique.
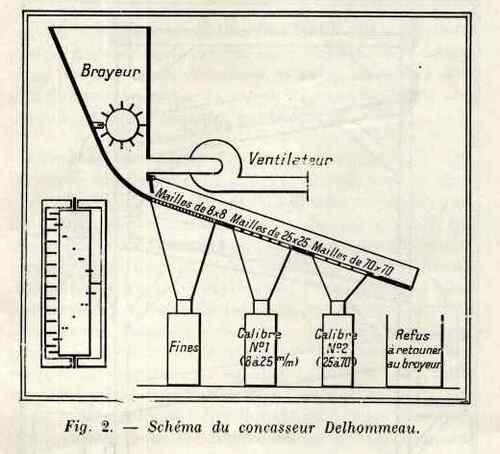
Humidité. - En raison de sa grande porosité, le charbon de bois présente une grande affinité pour l’eau : immergé, il peut absorber jusqu’à 50 % de son poids d’eau ; un séjour prolongé en atmosphère humide (brouillard, pluie) peut porter le poids d’eau absorbé par le charbon sec à 15 % ; au delà d’une certaine teneur, l’allumage devient difficile et on risque le colmatage des toiles filtrantes. Cependant, comme nous le montrerons dans notre prochain article, une certaine teneur en eau est loin d’être nuisible : le législateur a fixé à 8 % le poids d’eau maximum au moment de la vente.
Avec un peu d’habitude, on peut distinguer assez facilement un charbon sec d’un charbon humide : sec, le charbon a une cassure noire brillante ; humide, cette cassure est noire, terne ; le charbon sec rend un son clair, métallique, le charbon humide tombant sur un objet dur rend un son mat ; quand on vide un sac de charbon sec, il s’élève toujours une poussière légère, qui ne se produit pas si le charbon est humide.
Lorsque l’on a des doutes sur la teneur en eau, on pèse 1 kg. de charbon que l’on fait sécher dans un four de cuisine que l’on ouvre et on active le chauffage pendant 1 ou 2 h. : si après séchage le poids est inférieur ou même égal à 920 g., le charbon doit être rejeté, car, avec ce séchage imparfait, la teneur en eau est supérieure au maximum légal de 8 %.
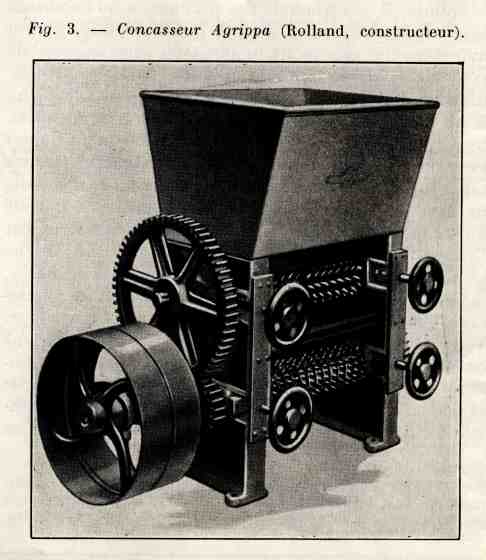
Emballage et stockage. - Du four au concasseur, le charbon est transporté en sacs de jute contenant de 25 à 40 kg. ; ces sacs doivent être mis sous bâche en temps de pluie.
Le charbon préparé pour gazogènes est livré en sacs de papier fort (papier Kraft) doublé de papier souple ; certains fabricants ont imaginé des caissettes en bois déroulé : les arêtes des faces sont réunies par une bande gommée de papier fort : un coup de couteau permet d’ouvrir la caisse facilement et la caisse vide peut se replier ; elle ne tient alors pas de place et peut être reportée au vendeur, alors que les sacs, souvent ouverts en arrachant les agrafes de fermeture, ne peuvent guère servir qu’une fois. Ces deux modes d’emballage protègent bien le charbon de l’humidité : il n’en est pas de même des sacs de jute, dont, en outre, la manutention n’est pas propre. Si l’on est obligé, à défaut d’autre emballage, d’utiliser des sacs de jute ayant contenu des produits chimiques (engrais, sel, soufre, sulfate de cuivre, de fer, etc ... ), ces sacs devront être préalablement lavés.
La forme et les dimensions prévues à l’article 4 de l’arrêté du 14 septembre permettent de dire qu’une tonne de charbon correspond à 70 à 120 sacs environ. Nous recommandons de ne pas mettre plus de 6 sacs les uns sur les autres, soit sur une hauteur de o m. 30 x 6 = 1 m. 80 : au delà de cette hauteur la manutention exigerait un escabeau et ’de plus, les sacs inférieurs, écrasés, contiendraient trop de poussières ou de menus. La longueur correspondant à un tas de 1 t. serait donc de : $$$ \frac{0m.30 \times 70}{6} = 3,50m$$$ à $$$ \frac{0m.30 \times 120}{6} = 6 m$$$
La longueur des sacs est d’environ 0 m. 70.
Le charbon doit être stocké dans un endroit sec ; les sacs ne seront jamais posés directement sur le sol, mais sur des madriers.
Rendements. -
Les fabricants de charbon de bois en usine ont coutume de donner la règle des quatre quarts, c’est-à-dire que d’une tonne de bois on peut extraire :
- 250 kg de charbon ;
- 250 kg de sous-produits ;
- 250kg de gaz ;
- 250 kg d’eau ;
Cette règle fait image, mais elle est assez grossièrement approchée, notamment en ce qui concerne les trois dernières catégories de produits.
De nombreux essais de fours ou meules métalliques ont été effectués, notamment à l’occasion de concours qui ont permis de comparer divers appareils ; mais les résultats peuvent différer de ceux que l’on obtient dans une exploitation industrielle : ici, les bois sont plus ou moins secs et sains, et la main-d’œuvre n’est pas sélectionnée comme lorsqu’il s’agit d’un concours.
Nous avons pu, dans un chantier organisé à la fois comme une exploitation industrielle et comme chantier-école ( [6]), effectuer diverses mesures de rendements par rapport aux volumes et - ce qui est plus rare pour des essais en forêt - par rapport aux poids de bois. Les résultats que nous avons obtenus figurent au tableau ci-annexé.
II a été fait usage d’un seul type de four, et de ce point de vue, les essais sont comparables entre eux.
Les bois traités, abattus depuis 12 à 15 mois, comprenaient en majeure partie du chêne, du hêtre, un peu de charme et de tremble et quelques éléments de bouleau ; ils provenaient d’une coupe de taillis sous futaie.
II ne nous a pas été possible de carboniser séparément les diverses essences, mais, somme toute, les essais se sont poursuivis dans des conditions habituelles d’exploitation.
Les bois ont été soigneusement mis en stères et pesés avant l’empilage dans les fours ; le tableau reproduit les résultats obtenus pour des échantillons de gros seurs diverses.
Les rendements à la tonne de bois ne donnent pas une indication de bien grande valeur ; nos pesées, effectuées d’octobre à décembre en forêt ont porté sur des bois parfois humides, donc accidentellement alourdis ; cependant on peut remarquer l’influence du poids spécifique ; si, dans la deuxième série d’essais, la charbonnette avait pesé autant que dans la première série, le résultat eût encore été amélioré. Nos opérations montrent que le rendement en poids peut varier entre 180 et 200 kg. à la tonne de bois ; exceptionnellement il pourra atteindre 220 kg. ; ce n’est qu’avec le chêne-vert, abondant en Provence, que nous avons pu atteindre 300 kg. : tonne de bois.
Le rendement au stère est plus intéressant car c’est le seul que l’on puisse établir en forêt, sauf en cas d’essais systématiques. Le tableau de nos résultats montre, comme il fallait s’y attendre, que le rendement croît en même temps que le diamètre des bois traités, sous réserve, bien entendu, que les gros bois soient sains. On remarquera en effet que, dans les deux premiers groupes d’essais la charbonnette est soit traitée seule, soit prépondérante, mais dans les trois autres groupes, il faut considérer que la charbonnette a servi surtout à confectionner la cheminée et le caillebotis, à garnir quelques vides, notamment au sommet de l’édifice de bois, et à allumer.
Le meilleur rendement a été obtenu avec la proportion 1 st. de charbonnette et 3 de rondins.
Nous soulignerons le fléchissement des rendements dans le cinquième groupe où nous avons traité simultanément charbonnette, rondin, quartier (bois de plus de 15 cm. de diamètre fendu en deux ou quatre, suivant la grosseur) ; nous pensons que la carbonisation « à cœur » des gros bois a nécessité une dépense plus élevée de combustible, qui a été fourni non seulement par la charbonnette, mais aussi par le rondin : nous avons déjà signalé qu’il était contre-indiqué de placer des bois minces près de gros bois.
Nous avons pu, suivant les circonstances, étudier d’autres bois :
- à Cadarache (B.-du-R.), nous avons produit 55 kg. de charbon brut par stère de genévrier (80 ans) et 100 kg. et plus par stère de chêne-vert ;
- en forêt d’Avallon, nous avons obtenu 65 kg. de charbon brut par stère de résineux.
A défaut d’autres précisions établies par nous sur les résineux, nous citerons les chiffres donnés par M. Pallu, ancien Inspecteur principal des Eaux et Forêts à Mont-de-Marsan. Il a obtenu, comme rendements normaux, par stère de bois de pin maritime, 69 kg. de charbon brut et 56 kg. de charbon concassé, criblé, dépoussiéré.
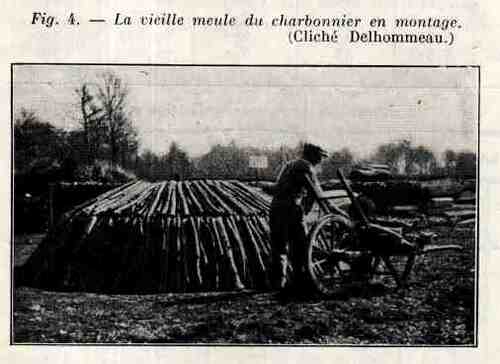
Rappelons encore que l’état du bois a une grosse importance : nous n’avons pu produire que 55 kg./st. de charbon brut avec de la charbonnette piquée au point qu’un rondin de 5 cm. de diamètre pouvait être brisé à la main par un choc un peu énergique ; signalons aussi que, en forêt d’Arques-la-Bataille nous avons produit 65 kg./st. (charbon brut), avec de la charbonnette de hêtre abattu 8 à 15 jours avant le traitement ; la cuisson d’un four de 4 st. demandait couramment 26 à 28 h., alors qu’avec du bois sec la même opération ne nous demande que 18 à 20 h.
Dans les dernières colonnes du tableau, nous avons fait ressortir la production d’un four de 4 st. : voisine de 300 kg. pour le charbon brut, on peut compter sur 260-270 kg. de charbon préparé pour gazogènes. Dans nos calculs ultérieurs, nous tablerons seulement sur 250 kg. par fournée, soit 1 t. de charbon préparé, pour 16 st. de bois : ce faisant, les exploitants ne pourront avoir qu’une agréable surprise : celle de voir la production dépasser les prévisions.
Nous donnons les tonnages produits en charbon n°1 et en charbon n°2 : ces nombres ont peu de valeur, car on peut, en réglant le concasseur, faire varier la proportion de l’un par rapport à l’autre.
Enfin, nous avons calculé la perte au concassage par rapport au charbon brut : elle dépend du concasseur et de la friabilité du charbon et varie entre 8 et 12 %.
Caractéristiques du charbon de bois.
- La densité de chargement ou poids de 1 m³ de charbon préparé pour gazogène influe sur le rayon d’action-chargement ; elle varie avec l’essence d’origine, le calibre et la teneur en eau.
Pour montrer l’influence de l’essence, nous citerons deux mesures que nous avons pu faire sur charbon de même calibre (n° 1) ; le charbon de genévrier pesait 155 kg/m3 et le charbon de chêne-vert 307 kg/m3. Ce dernier charbon, en calibre n° 2, pesait 295 kg/m3.
En laissant de côté ces cas extrêmes et assez particuliers, ces essences n’étant répandues que dans certaines régions de la France, la densité du charbon de bois varie de 180 kg/m3 pour les charbons de bois tendres ou résineux, à 270 kg. pour les charbons de bois durs.
La résistance mécanique est rarement déterminée ; on a proposé de mesurer la charge d’écrasement suivant la direction des rayons médullaires, en fixant comme limite, un peu arbitrairement sans doute, la charge de 14 kg/cm2. Il nous semble préférable d’user du procédé employé pour la mesure de la dureté des pierres : placer un poids donné de charbon calibré dans un tonneau auquel on fait exécuter un certain nombre de tours dans un temps déterminé et passer au tamis correspondant au calibre initial : le pourcentage des refus donnerait une idée plus précise, plus parlante, de la dureté, ou plutôt de la friabilité du charbon.
Cendres. - On peut déterminer approximativement la teneur en cendres : mettre 1 000 kg. de charbon sec sur une plaque de tôle et chauffer de manière à allumer le charbon et le laisser brûler complètement, au besoin en continuant à chauffer ; peser le résidu cendreux. Pour obtenir une mesure précise, il faut recourir à des méthodes de laboratoire et définir les conditions de l’incinération ; si en effet le bois con tient des carbonates, ceux-ci se dissocient à une température déterminée et dans ces conditions, il y a lieu de rester au-dessous de cette température. L’essai que nous indiquons doit donc être fait à température aussi basse que possible.
La teneur en cendres dépend du terrain qui a porté le bois carbonisé. L’arrêté du 14 septembre 1940 fixe comme limite maximum 5 % de cendres ; les charbons à teneur supérieure pourraient cependant être admis dans les gazogènes, sans autre inconvénient que d’entraîner des décrassages plus fréquents, et il semble qu’il eût été possible d’autoriser ces charbons avec une réfaction de prix selon la teneur en cendres : les cendres sont moins dangereuses que les goudrons, au sujet desquels l’arrêté reste imprécis, ou tout au moins n’indique qu’une tolérance, alors que les gazogènes à foyer volumineux peuvent s’accommo der d’une proportion, asez faible d’ailleurs, d’incuits.
Le pouvoir calorifique du charbon de bois, ou cha leur dégagée par la combustion complète du combustible, s’établit aux environs de 7 500 cal./kg. Il dépend non seulement du carbone fixe, mais aussi du carbone combiné (carbures d’hydrogène) et de l’hydrogène que, lors du refroidissement, le charbon a absorbé.
La porosité peut s’exprimer par la quantité d’eau ou de vapeur d’eau que le charbon peut absorber en un temps donné. Les charbons de bois tendres, résineux ou verts sont les plus poreux.
L’inflammabilité peut se caractériser par la température à laquelle il faut porter un combustible pour qu’il s’enflamme ; cette température renseigne, pour un taux d’humidité et un calibrage déterminés, sur l’aptitude aux départs rapides et aux reprises.
La combustibilité peut se définir par le temps nécessaire pour que le combustible enflammé soit réduit en cendres. Les charbons de bois durs sont moins combustibles, donc plus économiques, que les charbons de bois tendres.
L’inflammabilité et la combustibilité sont en relation étroite avec la porosité.
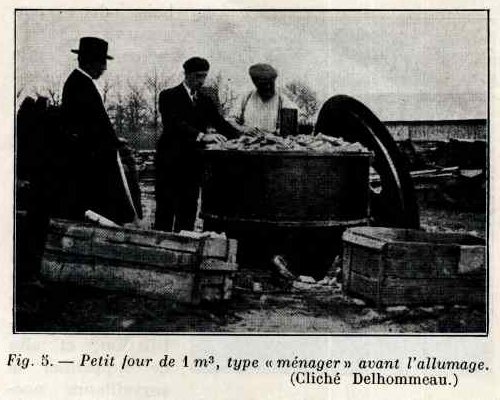
La réactivité est la faculté d’assurer la réduction du gaz carbonique en oxyde de carbone, ou la dissociation de la vapeur d’eau ; elle peut se définir par la température à laquelle il faut porter le combustible pour que les réactions s’amorcent. On a constaté que les charbons de bois étaient plus réactifs que les charbons d’origine minérale.
Ces trois dernières caractéristiques sont difficiles à déterminer : on n’est pas encore d’accord sur les méthodes à employer, ni même sur les définitions à donner. De plus, les essais de laboratoire faits jusqu’ici, ont porté sur de petites quantités de charbon et l’échantillon a dû subir une préparation qui a pu modifier ses propriétés industrielles. Nous ne nions pas la valeur des résultats obtenus en laboratoire, mais la pratique courante, qui ne vise pas à la recherche mais au contrôle commercial, nous paraît exiger les conditions d’essais suivantes :
- les épreuves devront porter sur un volume assez important de combustible ; les échantillons seront constitués par des charbons répondant aux spécifications de l’arrêté du 14 septembre 1940 ;
- les appareils d’essais seront simples et faciles à manipuler ;
- l’indice cherché devra être obtenu par une opération rapide et peu coûteuse, car cet indice ne sera, le plus souvent, valable que pour de faibles tonnages ;
- l’essai portera sur un prélèvement représentant l’élément moyen du lot entier soumis à l’étude.
À ces conditions, les résultats seront susceptibles d’avoir une influence réellement pratique sur l’exploitation et sur l’utilisation rationnelle du charbon.
Organisation d’un chantier de carbonisation.
- Nous considérerons un chantier de moyenne importance, en vue de la production d’environ 1 t. de charbon par jour.
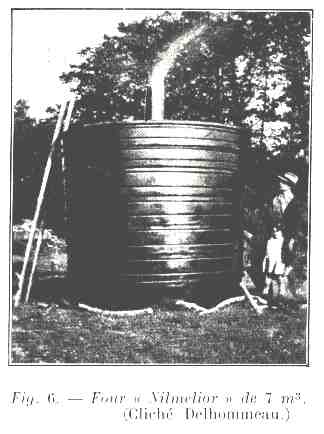
Nous préférons le chantier mobile au chantier fixe : ce dernier peut paraître avantageux, la carbonisation se faisant toujours sur le même faulde, mais il oblige au débardage du bois, particulièrement onéreux en terrain accidenté ; le chantier mobile, par contre, impose le transport des fours et l’aménagement d’emplacements nouveaux ; la dépense qui en résulte est cependant inférieure à la différence des prix de transport du bois et du charbon.
Le transport des fours sera d’ailleurs rendu moins pénible par le choix de modèles de 4 st. à 4 st. 5. Un tel four (4 st.) peut produire au moins 250 kg. de charbon préparé par cuisson, et l’opération dure 48 h. : pour une production de 1t. par jour, il faut donc 8 fours répartis en deux batteries, que nous numéroterons 1 et 2, de 4 fours ; une batterie sera allumée chaque jour.
Nous estimons que deux bons charbonniers peuvent défourner un four en 3/4 d’heure et le remonter en 1 h., s’ils trouvent le bois près du four ; en conséquence, on devra leur adjoindre, pour l’approche du bois, deux manœuvres, et même trois, si le terrain est accidenté.
La durée de la cuisson seule variant de 18 à 20 h., il faut que les fours soient allumés le soir vers 17 h., afin de réserver pour la nuit la période calme de la distillation, et afin de supprimer la surveillance nocturne. Cependant, sans astreindre un charbonnier à veiller, nous recommandons d’en loger un à proximité des fours, surtout à l’ouverture d’un chantier, alors qu’on ne connaît pas encore le comportement du bois à la carbonisation ; nous avons vu, lors du début de l’exploitation d’une coupe, que des fours allumés le soir, auraient pu être fermés à 3 h. ; se fiant à ce qui s’était passé dans d’autres chantiers, l’ouvrier avait trop ouvert les évents ; à l’arrivée du personnel le four fut éteint, mais la production fut faible.
Le matin, les charbonniers, tout en défournant une batterie, surveillent la fin de la carbonisation de l’autre, puis remplissent les fours vidés.
Voici le roulement que nous employons : le lundi matin, le personnel, moins un ouvrier, est au chantier et trouve 8 fours éteints pleins de charbon. L’ouvrier manquant rentre au début de l’après-midi ; voici le travail de chaque jour :
- lundi : défourner la batterie 1, la remonter et allumer le soir ;
- mardi : surveiller la cuisson de 1, tout en défournant la 2e batterie que l’on remonte et allume le soir ;
- mercredi : surveiller la cuisson de 2, défourner, remonter et allumer 1 et ainsi de suite. Les fours allumés le samedi soir seront surveillés le dimanche matin par un seul ouvrier, qui d’ailleurs s’occupera en outre à approcher du bois pour le lundi.
En principe, une telle organisation devrait assurer une production de 6 t. par semaine : en pratique, ce chiffre sera rarement atteint, car il faut prévoir que des fours pourront être à réparer, que la pluie pourra gêner les défournements, que les fauldes nouveaux seront à aménager. Une bonne équipe de 4 hommes, homogène, active, peut produire en moyenne 5 t. de charbon par semaine, avec 8 fours.
Chantier de concassage.
- On peut adopter diverses combinaisons :
a) pour une production de 1 t. par jour, constituer des équipes de femmes cassant le charbon à la main : 2 pour le cassage, et 2 autres pour charger les sacs, les peser, les fermer ;
b) pour une production de 5 t. par semaine, carboniser pendant 5 jours et, le samedi, employer le personnel à casser le charbon avec un concasseur mécanique ou un concasseur à main ; la manœuvre de l’appareil à main est très pénible et de plus, cette organisation immobilise un matériel coûteux pour une production irrégulière ;
c) concasser chaque jour, avec un appareil entraîné par un moteur de 3 ch. Son service demande un homme pour l’entretien du moteur et l’alimentation du concasseur, 2 femmes pour la fixation des sacs vides et l’enlèvement des sacs pleins, 2 femmes pour le pesage et la fermeture des sacs.
Généralement un appareil de ce genre a un débit journalier de plusieurs tonnes et dans les conditions de production du chantier, il est mal utilisé, mais qui ne connaît les avantages de la coopération : si certains propriétaires forestiers, particuliers ou communes, ne possèdent pas une forêt suffisamment grande pour que l’exploitation par un seul individu soit rémunératrice, ils peuvent se grouper, acheter ou louer du matériel en commun, s’unir par des liens suffisamment souples pour que chacun, coopérateur, coopérative, client, y trouve son intérêt. Il existe des coopératives de production, vinicoles, laitières ou autres qui sont prospères ; pourquoi n’en serait-il pas de même des coopératives forestières de carbonisation. Nous croyons d’ailleurs savoir que de telles associations sont en voie de constitution et nous ne pouvons qu’approuver un tel mode d’exploitation.
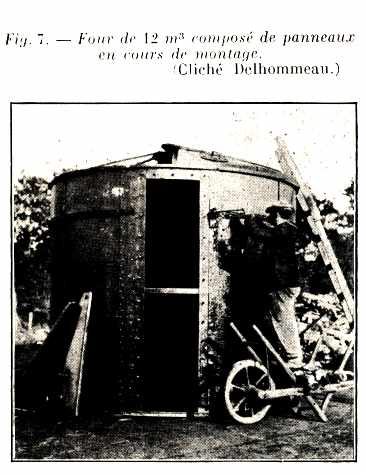
Au lendemain de l’armistice, nous avons été assailli de demandes de renseignements sur la fabrication du charbon de bois : tout le monde « s’intéressait particulièrement » à la question, pour des raisons faciles à comprendre : situation brisée, perspective de chômage, etc ...
La forêt, c’est entendu, peut être une puissante source d’énergie et devenir un vaste chantier où de nombreuses activités peuvent trouver à s’exercer, mais, après l’avoir dédaignée, il ne faudrait pas croire que la forêt, à elle seule, peut apporter un remède à tous nos maux ; ses possibilités sont grandes, mais limitées, elle ne peut subvenir aux besoins de tous nos véhicules, ni nourrir tous nos chômeurs.
D’après une statistique dressée en 1938 par l’Administration des Eaux et Forêts, la forêt française pourrait fournir annuellement en charbonnette (diamètre de 1 cm. 5 à 7 cm., les bois de diamètre supérieur, réservés au chauffage, ne devant pas, en principe être carbonisés) :
- de bois résineux : 1 754 000 st. ;
- de bois feuillus : 13 372 000 st.
Or, la loi du 6 août stipule :
En conséquence, la production annuelle doit atteindre à bref délai :
1 754 000 x 1,5 = 2 631 000 st. de charbonnette de résineux ;
13 372 000 x 1,5 = 20 058 000 st. de charbonnette de feuillus ;
soit au total : 22 689 000 st. de bois.
Si nous nous reportons aux chiffres précédemment indiqués pour les rendements :
les résineux fourniront : 0,055t x 2 631 000 = 144 705 t de charbon ;
et les feuillus : 0, 070t x 20 058 000 = 1 404 060 t de charbon ;
soit, au total : 1 548 765 t. de charbon concassé, calibré, dépoussiéré.
Soit maintenant un véhicule consommant 40 kg. de charbon aux 100 km. et couvrant 40 000 km. par an. Sa consommation peut être évaluée à : $$$ \frac{40 \times 40 000}{100} = 16000 kg / an$$$
La forêt permettrait donc d’alimenter : $$$ \frac{1548765}{16} = 100 000$$$ véhicules analogues
Ce nombre serait plus grand encore, si l’on tenait compte que certains gazogènes sont susceptibles d’être alimentés avec des charbons de terre.
Le gouvernement a cependant sagement décidé qu’il ne serait équipé que 50 000 véhicules à gazogène.
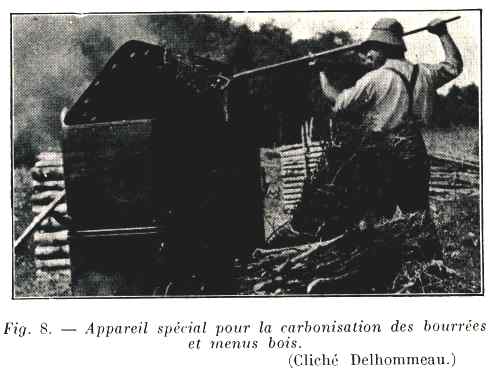
Il faut considérer que cela constitue une première tranche d’un programme plus vaste. Ce chiffre n’a d’ailleurs pu être arrêté qu’en tenant compte des possibilités des usines françaises pour la construction des gazogènes ct des fours. D’autre part, l’exploitation intensive de nos forêts, dans les conditions fixées par l’article 1er de la loi du 6 août, ne peut se poursuivre au delà de quelques années sans préjudice grave pour notre patrimoine forestier. Enfin, pour alimenter les véhicules régulièrement, il faut trouver la main-d’œuvre pour l’abattage, la préparation et la carbonisation du bois. Si l’apprentissage du métier de bûcheron et de charbonnier peut être très court, il est difficile de transplanter de la ville à la forêt de grandes masses de personnel : les problèmes du logement, du ravitaillement, de l’acclimatation sont complexes.
Admettons que tous les fours soient d’une contenance de 4 st., et qu’un four puisse faire 125 cuissons par an (250 jour de travail) : la fabrication du charbon exigerait $$$ \frac{22 689 000}{ 4 \times125 } = 45 000$$$ fours environ ;
comme 4 hommes peuvent servir 8 fours, le personnel affecté à la seule opération de carbonisation compterait :$$$ \frac{4 \times 45 000}{ 8} = 22 500$$$ ouvriers.
Le concassage de 5 t. de charbon par jour ou 5 x 250 = 1 250 t. par an occuperait :$$$ \frac{1 548 765}{ 1250 } = 1200$$$ personnes environ.
Enfin, un bûcheron professionnel peut façonner de 2 à 2 st. 5 par jour : supposons qu’un chômeur, après quelque temps d’entraînement, n’en produise que 1 st. 75 par jour ou 1,75 x 250 = 440 st. par an, la production du bois absorbera :$$$ \frac{22 689 000}{ 440 } = 52 000$$$ouvirers
La forêt pourrait donc fournir du travail à 22 500 + 1 250 + 52 000 = 75 750 chômeurs.
Il faut ajouter à ce chiffre, les charretiers, les affûteurs d’outils, le personnel de maîtrise, la main-d’œuvre nécessaire pour la confection des outils, des emballages : nous pouvons évaluer à environ 100 000, le nombre des chômeurs qui pourraient trouver du travail dans la préparation du charbon de bois et les industries annexes.
Cette possibilité de la forêt française n’a pas échappé aux pouvoirs publics : les Ministères du Travail et de l’Agriculture organisent des chantiers-écoles de bûcherons-charbonniers, et les initiatives de certains industriels désireux d’occuper leur personnel ont été encouragées. La Direction générale des Eaux et Forêts s’est préoccupée de faire de ses gardes forestiers des moniteurs de carbonisation, et nombre d’entre eux sont déjà capables de diriger un apprentissage, qui n’est, par lui-même, ni long ni pénible. Quant au Ministère du Travail, il procure aux chômeurs rééduqués, le logement, couvre une partie des frais de nourriture, verse l’allocation de chômage pendant toute la durée de la rééducation, assure le transport du chômeur et de sa famille de sa résidence habituelle au lieu de placement. Ces deux Administrations conjuguent leurs efforts et leur collaboration ne peut avoir que les meilleurs résultats.
Messages
1. Le charbon de bois, 13 septembre 2012, 08:19, par MEURGUES René
LE CHARBON DE BOIS
Bonjour,
Pouvez vous me donner le poids de gaz carbonique dégagé lors de la conbustion complète d’un kilo de charbon de bois ?
Merci de votre aimable réponse
Salutations
René MEURGUES
Association « Solidarité France-Madagascar »
5 rue des Jonquilles
14740 Bretteville l’Orgueilleuse
1. Le charbon de bois, 13 septembre 2012, 13:28, par gloubik
Bonjour,
La teneur en carbone du Charbon de bois varie, en fonction d’un certain nombre de critères dont la qualité du bois et le mode de fabrication, autour de 70 %.
Partant de cette valeur moyenne, on peut estimé la quantité de CO2 rejeté par la combustion de 1 kg de charbon de bois à environ 2,6 kg.